Introduction
Patient’s esthetic appearance is one of the mainly concern during the seeking of orthodontic treatment. Both brackets and wires were common place made of metals, such as stainless steel, cobalt—chromium or titanium alloys (Fallis and Kusy, 2000). All of them have the flexibility; strength and chemical resistance needed for orthodontic purposes as well are clearly visible to observers. In order to improve the appearance of fixed orthodontic appliances, and thus to increase patient acceptance, several aesthetic materials have been used as an alternative to metals in bracket and wire manufacture (Huang et al., 2003).
Until recently, coating metallic archwires with plastic resin materials was the main solution to provide aesthetic characteristics to wires with metallic or silver color appearance. Materials used in the coating process are Teflon® or epoxy resin (Elayyan et al., 2008). As patients prefer that shiny metal wires were not as apparent as opaque, an alternative could be archwires with transparent or translucent features (Watari et al., 1998). It has been recognized that an aesthetic archwire can be made from continuous fibers or polymer matrix (Kapila and Sachdeva, 1989). The material can offer aesthetic features with different mechanical properties, which can be changed when modifications are performed in the type of fiber material, fiber content or fiber arrangement pattern (Huang et al., 2003).
Fiber-reinforced composite (FRC) used mainly polymers for the matrix and unidirectional glass fibers for reinforcement, which is embedded in composite matrix.
The matrix material, which is available from PETG, PC, nylon6, nylon12, PUs offers the aesthetic feature of the composite archwire while the fiber reinforcement (E glass, S2 glass, and Kevlar) provides the mechanical properties suitable for use in Orthodontics (Imai et al., 1999). For example, by changing the fiber material, arrangement, diameter or the number of filaments, stiffness properties can be altered, and thus, the kind of engagement between the wire and the bracket slot (Huang et al., 2003). In addition, the reinforced polymer composites in particular have the potential to be highly biocompatible, whilst maintaining suitable mechanical properties (Schlz et al., 2011). Even when produced by mould polymerization or hot drawing, the FRC (glass/ PMMA) volume fraction fits well the Young’s modulus for clinical application while satisfy the rule of mixtures for composite systems (Watari et al., 1998).
Mechanical properties of orthodontic archwires can be measured using a three-point bending test (Fernandes et al., 2011). This evaluates the load-deflection properties, which are considered the most important parameters determining the biological nature of tooth movement (Fernandes et al., 2011; Krishman and Kumar, 2004), and provides information on the behavior of the wires when subjected to deflection in the horizontal and vertical directions (Elayyan et al., 2008; Kapila and Sachdeva, 1989). This paper reports an investigation into the mechanical properties and surface characteristics of fiber-reinforced polymer wires. The null hypothesis was that there were differences in the behavior of the different wires analyzed.
Material and Methods
Bending properties of four groups of orthodontics archwire were tested. A FRC wire (Groups 1, 3 and 5: Optis; TP Orthodontics Inc, IN, USA) and a nickel-titanium (Groups 2 and 4: Reflex; TP Orthodontics Inc, IN, USA) 0.016 in diameter were evaluated. All samples for testing were cut with pliers from the straightest section of the archwire to a size of 30mm.
The wires were tested according to ISO 15841:2006(E) (ISO, 2006) standard for 3-point bending tests. The span length of 10 mm, the crosshead speed of 6.0 mm per minute and the radii of fulcrum and indenter of 0.1 mm were used as suggested by ISO standardization for orthodontic wires mechanical tests. The load was applied with a universal testing machine (Emic DL 10000; Emic Co; PR, Brazil) to the middle of the test specimens, and the flexural strength values were recorded with Tesc software (Emic Inc). The distance between the indenter and fulcrum was 5mm. Deflection was carried out with a centrally-placed indenter moved by a computer-controlled stepper motor. Six specimens for each group were tested for deflections of 3.1mm (groups 1, 2 and 5), and 1.5mm (groups 3 and 4) at temperature of 37oC (except group 5), and the hysteresis curves produced on the charts recorder were compared. The surface of the FRC wires was observed by a Jeol JSM 5800 LV scanning electron microscopy (Jeol Co, Tokyo, Japan). The vertical and longitudinal cross-sections of the FRC wires were also analyzed after mechanical cutting and polishing.
Statistical analysis was performed with Graphpad Prism software version 4.0 (Graphpad Software, CA, USA). Descriptive statistics were calculated for each of the groups tested. A multi-factor analysis of variance (ANOVA) was applied to determine whether there were significant differences among the various groups. For the post-hoc test, the Tukey multiple comparison test was used. Significance for all statistical tests was pre-determined at p.05.
Results
SEM analysis of the FRC wire before and after the three-point bending tests has been done. After bending tests, until a deflection of 1.5 mm, the wires showed no significant changes in their surface structure and the morphology looked similar to the as-received material before the mechanical tests. Deflections near 2.0 mm have already showed changes in the morphology and breakages between the fibers and PMMA matrix union (Fig 1). A change in the mechanical properties might be the consequence.
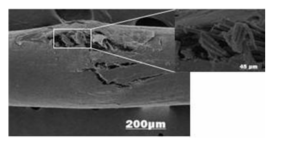
Figure 1 — Sem Images of Frc Optis Wire after Breakage in 2 Magnifications. Note the Fibers Release from Matrix after Fracture
The flexural load—deflection curves for wires were shown in figure 2. Curves (a) and (b) were the loading/unloading hysteresis loops for FRC wires under 3.1 mm deflection at 23±1oC and 37±1oC. They showed a slight difference in strength during loading and the breakage which occurred under a deflection between 1.5 mm and 2.0 mm. Curve (c) was the loop obtained for FRC wire under 1.5 mm deflection at the 37±1oC. The curve (c) was very similar to those of the deformation hardening type of superelastic NiTi wire before reach the loading plateau, however the flexural load required to produce a deflection of 1.5 mm on NiTi (group 4) was near double that for the FRC wires (table 1). By comparing loop (b) with that of loop (c) the effect of the breakage caused by flexural stress above 1.5 mm deflection became apparent under the unloading behavior of the FRC wires.
Table 1 — Descriptive Statistics (N) of Load Values of the Tested Groups (Each Group Contained 6 Specimens)
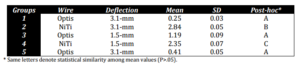
Table 1 showed the descriptive statistic results for the three-point bending tests results using various loading, unloading stages and temperatures. Maximum load values are given in newtons (N).
The results of ANOVA indicated significant differences among the groups (P <.0001) except between FRC groups (1,3 and 5) (p>.05). The highest force levels were recorded with the NiTi under 3.1 mm, followed by the same wire under 1.5 mm deflection. No significant differences were found between the Optis groups under different deflections and temperatures.
Discussion
The null hypothesis of the study was accepted since there were differences in the behavior of the wires mainly when submitted to different deflections. The maximum load values of NiTi wires were significantly higher than those of FRC wires under 1.5 mm and 2.0 mm deflection. This does not agree with other studies that disclosed similar mechanical behavior of FRC wires with different fiber fractions and NiTi under 3-point bending tests. (Huang et al., 2003; Imai et al., 1998)
In Figure 2 the flexural load-deflection curves of 0.016-in FRC under different deflections and temperatures are shown for comparison. The curves are similar until 2 mm of deflection when a failure is shown in FRC structure. When heated (37oC), FRC (b) showed a slight lower strength during loading when compared with the same deflection under 23±2oC (a), while similar curves (b,c) were seen during loading for different deflections under the same temperature (37oC). Probably, the influence of temperature may interfere with the molecular rearrangement of polymer chains. The glass fibers fracture can be seen in SEM picture (Figure 1). The curve up to failure of FRC wires should be regarded as the maximum load sustainable by the fibers was exceeded. FRC wires show after fibers breakage a great force decrease without elastic recovery followed by a curve and a great plastic strain. The curve demonstrated a low intensity hysterisis pattern below 0.5 N during unloading which might be associated with a residual flexural load of few fibers which could not be fractured during wire breakage. Failure in composite archwire was also described by predicted load-deflections curves during FRC fabrication (Huang et al., 2003). The breakage could have altered the loads reading during the bending tests which might result in the lowest load means and in the not significantly differences between groups 1 and 3.
Additionally, besides the volume ratio of glass fibers, the YoungÅ› modulus and the flexural load showed direct relation to deflection increase until a deflection nearing 2 mm. Beyond this level, a relation with the rule of mixtures was not even more supported. Above 2mm deflection, the mechanical behavior of the FRP may change, resulting in the increase of permanent strain in the hysteresis curve after unloading (Imai et al., 1998). The failure starts when the debonding and sliding at the interface fiber-matrix begins and becomes more remarkable. This situation was observed in this study for deflections above 2 mm.
Figure 2 also showed flexural load-deflection curves for a 1.5-mm deflection under 37oC. The deflection was decreased in order to not reach the glass fiber fracture point which was seen near 2.0 mm deflection. The FRC curves at unloading are similar to those of the deformation hardening type of superelastic NiTi wire under the same deflection. An excellent elastic recovery was observed and there is very little plastic strain. This agrees with other studies that evaluated with a 3-point bending test the force levels of composite orthodontic archwires (Huang et al., 2003; Imai et al., 1999; Imai et al., 1998). The viscoelastic behavior of the polymeric material could not be evaluated since during the bending test, there was not enough time to initiate the time-dependent response of the material during loading. A constant force should remain during sufficient time to allow the stress relaxation provided by the molecular rearrangement of the matrix polymer chains.
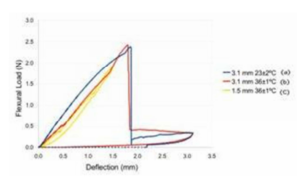
Figure 2 — Flexural Load-Deflection Curves of Optis Frc Wires under (A) 3.1-Mm and 23±2°C, (B) 3.1-Mm and 36±1°C and (C) 1.5-Mm and 36±1°C.
Three-point bending tests were carried out in accordance with the norms specified by ISO 15841:2006(E) (ISO, 2006). The force magnitudes were measured during unloading at 4 different deflection points after loading. The crosshead rate, number of specimens (n=6), permanent deflection, force magnitude and temperature were in accordance with the norm. Although the deflection suggested by ISO was 3.1 mm, this magnitude could not be performed with FRC wires due to breakage when deflected near 2.0 mm. However the efforts to analyze the mechanical properties of composite wires immediately before breakage, 1.5 mm of deflection could alter the bend test properties. As the mechanical behavior of FRC wires did not match with the ISO recommendations, maybe the inclusion in the standard of a new kind of wire type should be useful to represent the group of composite archwires currently available.
Superelastic Ni-Ti wires are widely used in the initial stage of orthodontic treatments12-14. Similarly to NiTi, intraoral fractures of FRC wires are located mostly in the posterior segment of the archwire due to the development of higher loading mastication forces, mainly when associated with wire spans which arise from the space provided by unerupted teeth or increased interbracket distance conditions (Bourauel et al., 2008).
The shape of the load-deflection curves of FRC showed a close linear loading and unloading behavior for deflections below 2.0 mm (curve c). The plateaus and hysteresis regarding the superelastic NiTi were not observed once these properties are mainly associated with phase transformation (Fernandes et al., 2011; Frenzel et al., 2010; Kim and Daly, 2011; Hou et al., 2011) which does not occur in FRC material. The figure 2 and table 1 demonstrated that FRC wires could cover the range of strength corresponding to the Ni-Ti wires under a deflection of 1.5 mm. For higher deflections than 2.0 mm, the strength of FRC is too low for practical use due to the partial sliding and unbonding at the interface between the glass fiber and PMMA matrix (Imai et al., 1998). Furthermore, previous investigations have reported the influence of the glass fiber fraction in the load-deflection wire characteristics (Fallis and Kusy, 2000; Watari et al., 1998; Imai et al., 1999; Imai et al. 1998). Maybe the fraction of glass fiber in the FRC analyzed in this study would contribute to the breakage observed for deflection near 2.0 mm. The possibility of breakage was reported by other authors who demonstrated similarity between FRC wires with an increased fiber fraction and NiTi during 3-point flexural test (Watari et al., 1998) under different deflections above 1.5 mm (Imai et al., 1998).
The fracture surface morphology of FRC wires showed a characteristic like pull out fail. During bending test the top surface of the archwire is compressed and the bottom is submitted to a tensile load in the longitudinal direction. The maximum tensile stress is in the bottom surface.
To explain the fracture surface morphology feature and the fracture mechanism it is necessary to analyze the stress distribution in the fiber and in the matrix. Fracture in polymer matrix composite is associated with the characteristic of fibers, matrix and interface. The mechanical properties of continuous fiber reinforced polymers are quite a bit higher in the longitudinal directions than in other directions.
The failure processes of the composite are fiber/matrix debonding, fiber pull out, fiber fracture, crazing and fracture of the matrix. In the present case the glass is a brittle material and is sensitive to the presence of any defect in the surface. Other evidences could be formulated from the analysis of in vivo fractured NiTi archwires from which is indicative of the brittle fracture pattern presumably due to the extremely high loading rate, which precludes plastic deformation to occur as a stress relieving mechanism (Bourauel et al., 2008). Unfortunately, there is a trade-off in properties, since the higher-stiffness FRC wires exhibit lower ductility. Thermoset FRC wires are brittle and might lead to fracture under mouth conditions and also have limited secondary formability. Another limitation of FRC wires is their unidirectional (anisotropic) properties, displaying relative weakness in shear (Burstone et al., 2011). Furthermore, the contact between fibers can induce a crack nucleation. When the crack reaches the polymer matrix, it can run into a direction parallel to the stress by traveling along the fiber-matrix interface, which is often weak in tension. The weak fiber-matrix interfacial bond strength explains the failure mechanisms show in the figure 1. This type of failure known as pull out fiber. The fibers run parallel to the archwire length.
In Figure 1 we can see that the fiber’ surface is clean; there is not any material from the matrix adhesive. A simple force balance along the fiber length gives:
σ π r2 = τ 2 π rl.
Where “σ” is the tensile stress in the fiber, “r” is the radius of the fiber, “Ï„” is the shear stress in the interface fiber-matrix and “l” is the length of the fiber. In the equation, the left side is the fiber strength and the right side is the interface strength (Chawla, 1998). The pulled out failure mechanism occurs when the interfacial shear strength is lower than the tensile strength of the fiber. Fiber reinforcement has success if the loading force can be transferred from the matrix to the fiber. Possibly the archwire mechanical properties increases with fiber surface treatment before the impregnation with the matrix polymeric.
Conclusion
- The breakage of FRC fibers occurred under a deflection between 1.5 mm and 2.0 mm. The fiber material can be considered as linearly elastic until rupture.
- The failure occurs due to debonding and sliding at the interface fiber/matrix. The fibers reinforcement suffered pull out, stress travels along the fiber-marix interface and crack reaches the polymer matrix. This kind of failure is called pull out fiber.
- No differences were found between the FRC groups under different deflections and temperatures.
- FRC archwires might have the mechanical properties needed for use in orthodontics during mild irregular alignment situations.
References
Bourauel, C., Scharold, W., Jager, A. & Eliades, T. (2008). “Fatigue Failure of as-Received and Retrieved Niti Orthodontic Archwires,” Dent Mater 24:1095-1101.
Publisher – Google Scholar
Burstone, C. J., Liebler, S. A. H. & Jon Goldberg, A. (2011). “Polyphenylene Polymers as Esthetic Orthodontic Archwires,” American Journal of Orthodontics and Dentofacial Orthopedics 139:E391-E398.
Publisher – Google Scholar
Chawla, K. K. (1998). ‘Ceramic Matrix Composite, Composite Materials, Science and Engineering,’ Springer. Verlag.
Elayyan, F., Silikas, N. & Bearn, D. (2008). “Ex Vivo Surface and Mechanical Properties of Coated Orthodontic Archwires,” European Journal of Orthodontics 30: 661-7.
Publisher – Google Scholar
Fallis, D. W. & Kusy, R. P. (2000). “Variation in Flexural Properties of Photo-Pultruded Composite Archwires: Analyses of Round and Rectangular Profiles,” Journal of Materials Science: Materials in Medicine 11: 683—93.
Publisher – Google Scholar
Fernandes, D. J., Peres, R. V., Mendes, A. M. & Elias, C. N. (2011). ‘Nickel-Titanium Shape Memory Alloys,’ ISRN Dentistry 2011:1-6.
Frenzel, J., George, E. P., Dlouhy, A., Somsen, C., Wagner, M. F. & Eggler, G. (2010) “Influence of Ni on Martensitic Phase Transformationn in Niti Shape Memory Alloys,” Acta Materialia 58:3444-3458.
Publisher – Google Scholar
Hou, X. M., Yahata, Y., Hayashi, Y., Ebihara, A., Hanawa, T. & Suda, H. (2011). “Phase Transformation Behaviour and Bending Property of Twisted Nickel-Titanium Endodontic Instruments,” International Endodontic Journal J 44:253-258.
Publisher – Google Scholar
Huang, Z., Gopal, R., Fujiara, K., Ramakrishna, S., Loh, P. L., Foong, W. C., Ganesh, V. K. & Chew, C. L. (2003). “Fabrication of a New Composite Orthodontic Archwire and Validation by a Bridging Mecromechanics Model,”Biomaterials 24: 2941-53.
Publisher – Google Scholar
Imai, T., Watari, F., Yamagata, S., Kobayashi, M., Nagayama, K. & Nakamura, S. (1999). “Effects of Water Immersion on Mechanical Properties of New Esthetic Orthodontic Wire,” American Journal of Orthodontics and Dentofacial Orthopedics 116:533-8.
Publisher – Google Scholar
Imai, T., Watari, F., Yamagata, S., Kobayashi, M., Nagayama, K., Toyoizumi, Y. & Nakamura, S. (1998). “Mechanical Properties and Aesthetics of FRP Orthodontic Wire Fabricated by Hot Drawing,” Biomaterials 19: 2195-00.
Publisher – Google Scholar
ISO 15841. Dentistry — Wires for Use in Orthodontics. ISO 15841:2006(E).
Publisher
Kapila, S. & Sachdeva, R. (1989). “Mechanical Properties and Clinical Applications of Orthodontic Wires,” American Journal of Orthodontics and Dentofacial Orthopedics 96: 100-109.
Publisher – Google Scholar
Kim, K. & Daly, S. (2011). “Martensite Strain Memory in the Shape Memory Alloy Nickel-Titanium under Mechanical Cycling,” Experimental Mechanics 51:641-652.
Publisher – Google Scholar
Krishnan, V. & Kumar, K. J. (2004). “Mechanical Properties and Surface Characteristics of Three Archwire Alloys,” The Angle Orthodontist 74: 825—831.
Publisher – Google Scholar
Lee, Y. H., Lim, B. S., Lee, Y. K., Kim, C. W. & Baek, S. H. (2010). “Comparison of Transition Temperature Range and Phase Transformation Behavior of Nickel-Titanium Wires,” Korean Journal of Orthodontics 40:40-49.
Publisher – Google Scholar
Pandis, N. & Bourauel, C. P. (2010). “Nickel-Titanium (Niti) Arch Wires: The Clinical Significance of Super Elasticity,”Seminars in Orthodontics 16:249-257.
Publisher – Google Scholar
Schlz, M. S., Blanchfield, J. P., Bloom, L. D., Coburn, B. H., Elkington, M., Fuller, J. D., Gilbert, M. E., Muflahi, S. A., Pernice, M. F., Rae, S. I., Trevarthen, J. A., White, S. C., Weaver, P. M. & Bond, I. P. (2011). “The Use of Composite Materials in Modern Orthopaedic Medicine and Prosthetic Devices: A Review,” Science and Technology 71:1791-1803.
Publisher – Google Scholar
Thompson, S. A. (2000). “An Overview of Nickel-Titanium used in Dentistry,” International Endodontic Journal 33:297-310.
Publisher – Google Scholar
Watari, F., Yamagata, S., Imai, T. & Nakamura, S. (1998) “The Fabrication and Properties of Aesthetic FRP Wires for use in Orthodontics,” Journal of Materials Science 33: 5661-64.
Publisher – Google Scholar