Introduction
Serious threats associated with climate change, habitat destruction, over-use of resources, and the degradation of vital ecosystem functions has resulted in a call for collective action by civil society, public institutions and the private sector to promote action that will aid the transition to an economy that can operate within the carrying capacity of the natural environment. Ultimately this means the transition to a much more resource efficient economic system (Von Weizsackeret al., 1997; Hawken et al., 1999; WBCSD, 2000; Stern, 2007).
Although numerous innovative strategies have been proposed for the corporate sector (Porter and van der Linde, 1995; Hart, 1997; Hawken et al., 1999; Hart and Sharma, 2004; Hoffren and Apajalahti, 2009), to realize a full transformation transition will necessarily need to occur within the SME sector as well. SMEs typically comprise the majority of economic activity in both developed and emerging economies (Williamson et al., 2006; Vickers et al., 2009; Parilla et al., 2010).
Since 1998, the Eco-Efficiency Centre (EEC) of Dalhousie University (Canada) has worked with small and medium-sized enterprises (SMEs) with the expressed goal of “fostering sustainable competitiveness” within their operations (Eco-Efficiency Centre, 2009a).
With a specific focus on supporting SMEs to identify opportunities to enhance productivity, the underlying approach has been to optimize business resource use both in terms of efficiency (doing more with less) and effectiveness (material substitutions and/or modifications) (Côté et al., 2006). The driver for this approach has been two fold. The first was the recognition of the crucial role that SMEs play in many economies, particularly in more peripheral geographic regions.
Their contribution to gross domestic product, job creation, innovation and the promotion of entrepreneurship make them key players in any resource efficient transformation of the economy. The second — in light of the heavy focus on MNCs in the sustainability literature – was the desire to better leverage the knowledge held within the university to support the integration of sustainability and related environmental performance strategies into SMEs.
From a practical point of view creating change and increasing resource efficiency within the SME sector poses a unique challenge. Operationally, SMEs cannot be treated simply as smaller versions of large corporations. As noted by Côté et al. (2006) there have been numerous attempts to define concepts such as business sustainability and — more specifically – resource efficiency, and to create frameworks and guiding principles to aid in their implementation.
However, much of this guidance has been focused on the needs of large corporations and has not incorporated factors that relate to the particular characteristics of SMEs.
To support a more fundamental transition to resource efficient economies a different approach is needed. It needs to recognize the specific drivers and motivators within SMEs to embrace and apply new knowledge; applications that will ultimately evolve out of an SME’s ability to innovate (Gorman et al., 1997; Brown et al., 2007; Varis and Littunen, 2010;Parrilli et al., 2010) around the concept of resource efficiency.
This focus on resource efficiency is echoed in UNESCAP’s Greening of Economic Growth series (2009) where the term eco-efficiency is used for these kinds of improvements in resource use:
“eco-efficiency is a more general expression of the concept of resource efficiency — minimizing the resources used in producing a unit of output — and resource productivity — the efficiency of economic activities in generating added value from the use of resources.”
The concept of eco-efficiency was popularised in 1992 by the Business Council for Sustainable Development(Schmidheiny, 1992). BCSD presented the idea that although industrial innovation can contribute to environmental degradation, it may also be a key part of minimising the environmental consequences of economic growth.
Emphasizing that environmental benefits can be coupled with economic development, eco-efficiency can be viewed as a foundation stone for green innovation, innovation that guides businesses to make better use of resources, internally and at different points in the supply-chain (Schmidheiny, 1992; DeSimone and Popoff, 1997). The key tenets of eco-efficiency are:
- Reduce material intensity;
- Reduce dispersion of toxic substances;
- Maximise use of renewable resources;
- Extend product durability; and
- Increase service intensity.
Eco-efficiency is thus the optimization of material/energy resource use within the industrial supply chain, in terms ofextent of use – either temporally (i.e. it lasts a long time), or spatially (i.e. it can be replenished, recycled or reused indefinitely); and intensity of use. In addition, the applicability of use (i.e. using the optimal resource for an optimal purpose) will be included in this description.1
1 While some refer to this aspect as eco-effectiveness (McDonough, 2002), the OECD’s definition of eco-efficiency is “the efficiency with which ecological resources are used to meet human needs”, which — one could argue – could include this third component. |
It follows that if eco-efficiency — which is essentially resource efficiency — underpins much of the focus of green innovation, then it can be argued that the paradigms generally applicable to knowledge transfer and action with respect to innovation should also apply to eco-efficiency. As such, the intent of this paper is to present the development and outcome of one such approach.
Resource Efficiency as Innovation
Innovation has been recognized as playing a major role in environmental degradation through its contribution to increased economic growth and consumption (Porter & Van der Linde, 1995; Hart, 1995). However, innovation is also seen as a key to achieving a sustainable future based on access to goods and services that can be delivered within the carrying capacity of the broader ecosystem (Hart, 1997; Hawken et al., 1999).
Much of the innovation literature focuses on large firms. They are seen to possess the financial resources, technical knowledge, organizational capacity and influence within the supply chain needed to drive significant innovation in environmental products and services (McAdam et al., 2010). However, there is an increasing number of studies concerned with the adoption of innovations by SMEs (Varis and Littunen, 2010), the role of SMEs in contributing to innovative resource efficiency solutions (Brown et al., 2007; Parrilli et al., 2010) and the specific barriers that may prevent innovation in SMEs (Könnölä and Unruh, 2007; Revell and Blackburn, 2007).
The advantage that SMEs have over large firms is that while large firms do indeed have the advantage of access to resources, SMEs have the advantage of flexibility and adaptability. Behavourially, SMEs can be more agile and responsive to information shifts that are seen as advantageous and/or necessary to maintain their competitiveness (Studer et al., 2006; Masurel, 2007; Borgaet al., 2009).
From their institutional involvement with Spanish SMEs, Parrilli et al. (2010) found that innovation in within that sector is more often associated with process or operational innovations and less associated with the development of patents or new product lines.
Such operational innovations tend to lead to improvements in resource efficiency such as reduction in the material intensity per unit output, or improved employee productivity. The driving motivations are often based on cost drivers.
For SMEs to contribute to sustainability at a level commensurate with their economic contribution, innovations will need to occur to a much greater extent than occurs currently. This transition is being enacted – albeit slowly – by policy and/or the changing expectations of consumers (Revell and Blackburn, 2007; Hoffren and Apajalahti, 2009). However, it is likely that resource scarcity and cost will be the most significant drivers in the future (Korhonen et al., 2004; Lovins, 2008). SME viability will have an increasingly direct relationship with the resource efficiency of both their internal processes and the supply-chains they choose to participate in.
However, while this eventuality is arguably inevitable (Côté et al., 2006; Lovins, 2008), there may exist a significant opportunity for those SMEs and the jurisdictions they exist within to achieve benefits, both in terms of competitive advantage and progress towards sustainability (Hawken et al., 1999; McDonough and Braungart, 2002; Stern, 2007).
This may be even more important for those SMEs that wish to compete internationally against businesses from jurisdictions where existing resource constraints have already prompted the adoption of more resource efficient strategies. As such, developing support mechanisms that accelerate how quickly a resource efficiency focus may enhance performance will be important in the transitioning to resource-use patterns that will improve society’s attainment of long term sustainability objectives.
Characteristics and Learning Dynamics of SMEs
According to Hillary (2000), Studer et al. (2006), Masurel (2007), Borga et al. (2009), and Vickers et al., (2009), SMEs can be broadly characterized by:
- A culture that is more dominated by the personal motivations of the owner or manager;
- Limited access to resources such as human and financial capital;
- Limited awareness of information/knowledge that is external to the specific day to day operational needs of the company;
- Preference for more personal or ‘informal’ management styles; and
- A general mistrust of external actors (particularly government officials and extension officers) and aversion to accepting the knowledge they are disseminating.
SMEs are known to provide “a unique and discrete location of activity…where it is possible to examine the evolution of situated practices and social relationships” (Zhang, Macpherson & Jones, 2006, p. 300). According to their internal learning processes and evidence of major changes being undertaken (e.g. new products, processes or relationships), SMEs are classified as either stable or innovative. For the most part, stable SMEs engage in experiential learning and focus on first-hand experience.
This has been concluded to be a result of such SMEs operating in mature industries with management systems that do not encourage information searching or knowledge sharing (Zhang et al, 2006). In general, stable SMEs tend to experience difficulty adapting to environmental change. Conversely, innovative SMEs — which are in the midst of launching new products, processes and/or relationships — predominantly learn via informational or interactive modes.
As their learning takes place, knowledge or information can be codified and accessed with relative ease. As well, knowledge is typically tacit and involves regular face-to-face social interaction (Zhang et al, 2006).
Over the past several decades, there has been an identifiable hierarchy within categories of learning based on the level of insight and association building (Fiol and Lyles, 1985). The two general levels are lower- and higher-level learning, both of which can be found within SMEs.
Lower-order learning refers to the learning that takes place within a given organizational structure governed by a set of established rules. It leads to the development of basic associations between behavior and outcomes. However, these are typically of short duration and impact only a small component of the organization. This type of learning is a result of repetition and routine and generally involves incremental developments (Fiol and Lyles, 1985).
In contrast, higher-order learning strives to adjust overall rules and norms as opposed to altering specific activities or behaviours. Therefore, the resulting associations have longer term effects and impacts on the entire organization. This type of learning generally takes place via the use of heuristics, skill development, and insights.
Thus, it is considered to be a more cognitive process in comparison to lower-order learning (which is usually the result of repetitive, stable behaviours) This type of higher-order learning dynamic is what one would expect to be present in SMEs that can address improved sustainability through taking a more innovative approach.
This is similar to the argument by Tosey et al. (2011) who distinguished between types of organizational learning that are either linear in nature (single loop) or allow for a questioning and re-evaluation of the organizations underlying assumptions and beliefs (double/triple loop).
Regardless of the specifics of the language being used, Senge and colleagues (2001) noted that, “the challenges of building sustainable enterprises describe a strange new world few [.. ] are equipped to understand” (pg. 36) and suggested the integration of such organizational-learning principles and tools could make the difference in addressing such development within businesses (Senge et al., 2001).
The Absorptive Capacity for Learning on Resource Efficiency in SMEs
In 2000, Hillary noted that the SME sector was:
“Largely ignorant of its environmental impacts and the legislation that governs it; oblivious of the importance of sustainability; cynical of the benefits of self-regulation and the management tools that could assist it in tackling its environmental performance; difficult to reach, mobilise or engage in any improvements to do with the environment”.
Since that time, it would seem that not much has changed (Borga et al., 2009; Parker et al., 2009; Vickers et al., 2009). Despite on-going efforts by policy makers and researchers alike to present the business case for sustainability (Côté et al., 2006; Revell and Blackburn, 2007; Eco-Efficiency Centre, 2009b; Eco-Efficiency Centre, 2010), many SME managers see environmental measures as costly and are therefore reluctant to take action voluntarily. Within the SME sector there appears to be a disconnect between the ‘codified knowledge’ related to resource efficiency that exists externally to SMEs — represented by its prevalence with the scholarly and institutional literature – and its ultimate integration as ‘tacit’ knowledge within these operations.
In the absence of tacit knowledge related to resource efficiency, this type of ‘innovation’ cannot be readily embraced. The level of related tacit knowledge underpins the willingness of organizations to embrace a particular change (read innovation) (Howells, 1996; 2002).
SMEs that find it easier to embrace change will be more willing to innovate (Parrilli et al., 2010). The ability of a business to absorb and apply new or externally supplied knowledge (and therefore change operational norms) is sometimes referred to as their absorptive capacity (Sparrow et al., 2009). The analysis of the innovation management literature completed by Bessant et al. (2005) suggested that a business’ absorptive capacity will fall into one of four categories:
1.Ignorance of key issues;
2.Awareness of key issues;
3.Knowledge and understanding of key issues and solutions; and
4.Implementation of key issues and solutions.
Bessant and co-workers (2005) discuss different approaches to developing absorptive capacity according to the particular state of the business at the time. While Bessant and colleagues did not have a specific focus on issues of sustainability, one can see how an understanding of SMEs’ absorptive capacity could influence the creation of support systems to facilitate knowledge transfer as it relates to green innovation and resource efficiency. Specifically, Vickers et al. (2009) highlight that previous research into SMEs’ absorptive capacity, as it relates to sustainability and related issues, suggest that most fall in category 2 — awareness of issues — but fall short of having any understanding of how to contribute to or implement solutions (Drake et al., 2004; Gray, 2006; Revell and Blackburn, 2007).
Other research has built on this notion of absorptive capacity in the development of green innovations within SMEs (Hansen et al., 2002), and explored the processes by which various environment-related influences (Gray, 2006) and sources of new knowledge were assimilated and applied within SMEs (Zahra and George, 2002; Hughes and O’Regan, 2009; Huggins and Johnston, 2009). Consistent with Bessant et al. (2005) the higher the absorptive capacity of the SME the more effective the knowledge transfer leading to better integration of green issues into their strategies. As such, any move to support such knowledge transfer must focus on increasing the absorptive capacity of SMEs, enhancing their ability to understand and then modify their operational norms and underlying assumptions.
This in turn, enhances the successful transfer of new knowledge within the SME. There is a positive reinforcement resulting from this relationship between learning dynamic, absorptive capacity and successful knowledge transfer and leads to a virtuous cycle of ever increasing capacity for embracing innovation.
A Potential Role for Higher Education Institutions (HEIs) in Technology Transfer for Resource Efficiency Absorption, Learning and Innovation in SMEs
Based on analyses of specific environmental adoption processes, Hansen et al. (2002) suggest knowledge transfer is influenced through a ‘dynamic triangle’ framework that includes:
- Strategic Orientation — the level of importance of environmental issues within the external network – as perceived by the SMEs;
- Network Relations — the level of competency found within the SME’s network related to knowledge about solutions to issue of concern; and
- Internal Competencies — the ability of SMEs to adjust to new ideas and approaches (pg. 39).
In a similar fashion, Parrilli et al. (2010) discuss a ‘tripartite innovation’ framework that considers:
- Critical Mass of Actors — the necessity for there to be a cluster of actors to drive integration of innovative ideas;
- Innovation Structures — networks of actors intent on supporting innovation in a collective manner; includes financiers, policy makers, knowledge institutions, etc…; and
- Learning Process — opportunities for experiential learning and the support for others to gain knowledge from the experiences of actors within their networks.
Drawing from these examples and others (Ashford et al., 2002; Gray, 2006; Etzkowitz, 2008; Hoffren and Apajalahti, 2009; McAdam et al., 2010), it can be generalized that knowledge transfer within SMEs is based on three pillars:
- Good linkages with external sources of knowledge (both codified and tacit);
- An external culture that supports innovation; and
- An internal culture that is capable of integrating and adjusting to new ideas.
Thus processes put in place to support innovation, higher-order learning and continued increase in absorptive capacity — whether via policy makers, industrial associations, or other actors (e.g. NGOs and knowledge institutions) – will need to understand and work to positively influence these three pillars.
Traditionally the role of the universities and/or higher education institutions (HEIs) with respect to contributions to industry has focused on support for policy development, scientific research and new technology development.
National innovation strategies and the ‘triple-helix’ concept noted by Etzkowitz and Leydesdorff (1997; 1998; 2000) have recognized the importance of this role and suggest specific linkages between university, industry and government should be increasingly to be leveraged to promote knowledge transfer.
However, such models are often quite linear where the innovation and technology transfer led by HEIs is through a process of applied research (i.e. specifically intended new knowledge creation) and development (i.e. resultant application and commercialisation) (Sparrow et al., 2006).
However, as noted previously, there is evidence that some forms of innovation (such as sustainability-focused or green innovation) often occur through the application of non- linear models; particularly true of SMEs.
As such, traditional HEIs can be less suited to this type of challenge, particularly in the case of SMEs. For example, HEIs do not typically have a portal for interaction with SMEs (and as such cannot easily be a source of external knowledge). As well, HEIs tend to deal with industry/businesses one at a time in a confidential, intellectual property constrained manner (and therefore cannot easily influence the external culture within which SMEs operate).
Perhaps most importantly are the unique constraints regarding knowledge transfer within SMEs and the fact that HEIs do not typically engage in research that investigates barriers to this type of knowledge transfer. This is quite apparent from the dearth of literature around green innovation within SMEs (Hughes and O’Regan, 2009; McAdam et al., 2010)).
Hughes and O’Regan (2009) have assessed the impact that the source of knowledge had on the knowledge transfer within SME manufacturers. They found that despite being a source of extensive codified knowledge around the ‘business case’ for innovation that could prove vital to the sector, HEIs were often seen as remote and inaccessible.
This severely limited their capacity for facilitation successful knowledge transfer that depends on transforming externally sourced codified knowledge into internally accessible tacit knowledge that SME managers could then put to use.
Along similar lines, Hart and Sharma (2004) suggested innovation necessitated businesses to include the views ‘fringe stakeholders’ in their management decision making. In this case, the emphasis is on the co-evolution of a structure that is put in place to identify, explore, and integrate the views of stakeholders on the fringe for the purpose of managing change and building innovation in their business model (Hart and Sharma, 2004).
One could argue that codified knowledge held in HEIs could be considered fringe from the perspective of SMEs who are not familiar with it and under normal operational circumstances would have no mechanism to easily access it. Therefore the role emerges for HEIs to transition themselves away from the fringe into a more accessible source of knowledge.
In addition, HEIs have demonstrated limited ability to integrate such information internally. They have not, for example, typically integrated this into their business and management curricula. They therefore do not have a meaningful influence on the development of knowledge and expertise within practitioners; expertise that would allow them to better address issues of sustainability.
Wheeler et al. (2005) noted that – both at the student and senior executive level – there have been few examples of successful transitions within management education to provide integrated offerings of business and sustainability learning, even in conventional corporate case studies. Springett (2009) suggests not much has changed. So it is entirely unsurprising that SMEs — which are typically excluded from management education anyway — do not have management education and sustainability resources.
From the foregoing arguments and a growing body of literature, we may asserts that there is an opportunity for HEIs to take on a new role within innovation systems and in the provision of support of knowledge transfer within the SME sector on resource efficiency. For example, Gunasekara (2006) suggests that although there has been a predominant focus in the literature on the analysis of university-industry technology transfer, there is an emerging body of literature that suggests there is a role in regional innovation systems — innovation systems that are specifically leveraged for regional economic development.
This role could include a much more active involvement in supporting knowledge transfer in a more horizontal approach whereby knowledge dissemination is delivered to a broader audience with a specific focus on ensuring its uptake and absorption. Both Huggins and Johnston (2009) and Parrilli et al. (2010) note the potential importance of HEI in the creation of effect knowledge networks that impact innovation and growth within regional SME sectors.
A Novel Knowledge Transfer Framework for SMEs and Resource Efficiency
Recognizing the burgeoning opportunity for universities and other learning institutions to address this knowledge transfer gap for SMEs and create suitable knowledge networks, the Dalhousie University Eco-Efficiency Centre was founded an outreach and research unit with the specific aim of fostering sustainability within the SMEs sector (Eco-Efficiency Centre, 2009a).
It is designated to act as an interlocutor between various stakeholders and knowledge providers (including academia, industrial organizations, non- governmental organisations, etc.) with the specific intent of: a) promoting the transfer of applicable knowledge from sources largely seen as ‘inaccessible’ to SMEs; b) supporting the development of peer networks capable of disseminating and promoting the ‘benefits’ of resource efficiency; and c) giving individual SMEs the tools and guidance to integrate such information into their day to day operations and longer term operational strategies. The primary focus was the SME manufacturing sector of Nova Scotia, an economically challenged and geographically peripheral Province of Canada.
The idea was that the combined acumen of business and engineering academics, policy experts and environmental management researchers could be brought together to deliver practical, best practice oriented information for SMEs that would be easy to access and viewed objectively. The intent has been to promote an interdisciplinary space, that integrated student outreach activities and academic research to developed learning sessions focused on the ‘business case’ for resource efficiency used to build trust and credibility around this agenda within the SME sector of Nova Scotia.
The Eco-Efficiency Program for Manufacturers (E2PM), the flagship initiative of the EEC operated fully from 2005 until March 2009 2 3. The initiative focused on increasing awareness with SME manufacturers/processors about the business benefits that could be realized through pollution prevention and resource efficiency. It also intended to stimulate and support the implementation of related green innovations. Specific objectives were:
2 A pilot was initially run in 2003 but was not operationalized in its final form until 2005.
3 The original title of the initiative, the Eco-Efficiency Business Assistance Program (E2BAP), was changed to E2PM in 2008 to better reflect the fact that the program was singularly focused on providing support to SME manufacturers and processors.
|
- To provide SMEs with information to understand environmental issues pertinent to their operations, to build awareness of energy and materials efficiency, pollution prevention, and other related approaches and tools, and toaccelerate the awareness and adoption of resource efficiency-based innovations (thus influencing the third pillar — an internal culture capable of change);To improve business profitability and environmental performance of SMEs in Nova Scotia through the implementation of resource efficiency;
- To identify specific opportunities for improving environmental performance of participating businesses and determine technical feasibility and economic viability for the most promising opportunities (pillar one — supporting a link to external knowledge sources;
- To clearly demonstrate resource efficiency provides an economic benefit to the business;
- To develop case studies demonstrating the benefits of resource efficiency projects (pillar one); and
- To build further capacity within the industrial sector in the areas of resource efficiency improvement (pillar two — an external cultural supportive of resource efficiency).
There were four primary components of the program; two delivered directly by Eco-Efficiency Centre researchers and two developed by the EEC but delivered by approved consultants tasked with carrying-out the specific program requirements. EEC provided oversight and quality assurance for these later two components.
The ‘energy and environmental reviews’ introduced businesses to various strategies and practices that could improve resource efficiency such as the avoidance or minimization of waste (pollution prevention), and resource and energy conservation strategies. It also included an evaluation section to gain insight to current operations and attitudes as related to resource efficiency. These were completed by EEC researchers and students.
The ’opportunity assessments’ (OA) were aimed at identifying opportunities to improve resource efficiency within the various operational settings of the facility. Consultants completed activities such as data collection, identification of specific opportunities and the related potential savings, preliminary cost estimates for implementation, and recommendations for next steps. It also included a similar attitude query as noted in Component 1.
Following from the OA, participants could follow on with an ‘implementation assessment’ (IA) again involving a registered consultant. This involved detailed analysis of the costs, benefits and constraints associated with the specific opportunities identified in Component 2. It provided a detailed assessment of the technical feasibility, environmental impacts and benefits, projected savings, capital costs, pros/cons of implementation and recommendations for action.
A separate but equally important component of the program was the ‘industrial outreach’ activities carried out by EEC researchers and students. This component delivered in an on-going manner by the EEC, this involved the active dissemination of resource efficiency ‘success stories’ at manufacturing sector focused meetings, conferences and workshops. Where possible, local examples of participant successes were used.
However, also included was information related to specific resource efficiency opportunities for particular industrial operations, processes or equipment, successes realized by SMEs in other jurisdictions, notable cases of behavior shifts within SME operations, and research emerging from academia that was applicable to the audience.
While it was usually suggested that participants utilize all components, the only obligation was the necessity of completing an Opportunity Assessment (OA) prior to being permitted to complete an Implementation Assessment (IA).
Participation in the program was promoted within the SME manufacturers/processors of Nova Scotia at a number of levels. EEC researchers contacted companies directly — particularly those companies that were known to be high resource consumers (water, materials or energy), or producers of significant volumes of waste (solid, liquid, wastewater and/or hazardous waste).
In addition, the program was advertised by different government departments to industrial sectors as well as by numerous industry and business associations such as the Canadian Manufactures and Exporters (CME), various chambers of commerce and local regional development authorities. Once a business expressed interest in the program, it was directed to choose from a list of registered consultants who had been advised and vetted by the Eco-Efficiency Centre.
The two (the business and the consultant) created a proposal that was submitted to the EEC for approval. In some cases, the businesses already had potential opportunities in mind that they wished to have the consultant investigate in greater deal. However in most cases, the consultants were asked to do a complete overview of the facility to identify opportunities at a more holistic level. The businesses then were able to focus on specific opportunities in the subsequent implementation assessment.
Limited program funding meant that only participants who engaged in an Implementation Assessments (IA) were contacted for follow up approximately 6 months after the IA report was issued.
The rationale was that if the participant completed both and OA and an IA a higher likelihood that recommendations had been implemented. Participants were asked to highlight key initiatives they had undertaken and to provide any data (quantifiable or anecdotal) on the benefits of the initiatives. They were also asked about their experience with the program, what further steps they planned and what if any additional informational support could be useful. Where appropriate, participants were asked to supply testimonials about their experience.
This information was used to generate case studies and fact sheets that were in turn disseminated to other program participants -for example, those whom had not yet implemented any of the recommendations – as well as presented at industry focused conferences, workshops and information session in order to demonstrate the practical and realistic benefits available to SMEs through resource efficiency.
The intention was to support each of the three pillars necessary for knowledge transfer within SMEs noted previously, by a) gradually demonstrating the benefits that others in the sector had realized (thereby supporting the ‘external culture that supports innovation’); b) being accessible to new SMEs that were interested in learning more about the potential implications for them (thereby promoting the ‘good linkages with external sources of knowledge’; and c) to provide ongoing support to SMEs that still needed convincing that the opportunities that had been identified in their initial assessments were legitimate (thereby supporting the development of ‘an internal culture that is capable of integrating and adjusting to new ideas’).
During the program, the metrics utilized to demonstrate success were the “potential savings” that were identified for each participant. Each OA provided a cost/benefit for each recommendation and where possible outlined the savings in dollars, GHG, waste volumes, and/or fuel/energy savings (e.g. kWh or L). Table 1 provides an overview of the key indicators.
Table 1: Potential Program Benefits Identified in Recommendations
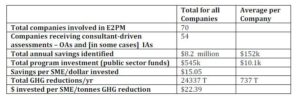
These ‘potential’ benefits were tracked throughout the program, revealing the possibility for impressive returns for tax dollars invested in the program. For each dollar invested in the program approximately $15 in annual savings were identified. With regards to GHG emissions reduction, the program cost per tonne of potential annual GHG reduction was calculated to be $22.39. However, these benefits were only hypothetical. Beyond the limited follow-up (previously noted), there were no information gathered that provide insight to the levels of impact the program had had on the SME sector.
This promoted the work discussed in the next section that endeavored to confirm the level of impact this program had. The intent was to determine whether the process developed to support knowledge transfer in this area of ‘green’ innovation and resource efficiency was successful and — if possible — to what degree it modified the norms by which the participants operate.
Methodology
In 2010, the 54 SME manufacturers that had participated in the E2PM program and had completed other OAs or IAs4were contacted. In each case, interviews were requested for the purpose of cataloguing all the recommendations provided as part of E2PM that were implemented and to determine what if any new initiatives were planned that were not directly recommended during the assessment process. The intention was threefold:
4 The responses from the sixteen participants that did not have at least an Opportunity Assessment completed by a consultant will not be included here. The EER conducted by the EEC research staff and graduate students was not designed to provide recommendations with quantifiable potential savings. As such it would be impossible to determine any direct causal relationship drawn between energy or environmentally focused initiatives undertaken by the company and their engagement with the EEC. Although there was anecdotal evidence to support the notion that their involvement with the EEC’s programs prompted them to undertaken eco-efficiency activities it could not be demonstrated directly.
|
- To gather data related to the empirical impact of the program experienced by each participant – in terms of cost savings, and GHG and waste reductions (primary motivator);
- To better understand attitudes towards the program and its perceived utility to them; and
- To gain insight to the participants’ internal culture and the level to which resource efficiency awareness had been built into their day to day operations – as compared when they first participated in the program.
The interviews were conducted in a semi-structured format where specific questions related to the uptake of E2PM recommendation were asked, followed by more open ended questions designed to evaluate the participants attitude towards opportunities and barriers related to internal sustainability initiatives in general.
Prior to each interview the recommendation reports were reviewed and the specific recommendations (along with the associated expected savings) were noted. The participant was then queried about which — if any — of the recommendations had been implemented and the driver for the decision.
It is recognized here that there was the potential for some interference due to interviewer effect, but the questions were asked in such a way as to require the participant to provide detailed information and quantifiable data where possible regarding what recommendations were implemented and how. While it is possible that participants embellished about the level of uptake, the interviews were completed by individuals familiar with the program, but who were not involved in the original assessments as to avoid as much as possible the desire on the part of the participant embellish their responses. Where available, actual empirical data related to cost savings, energy savings or waste volume reductions was gathered. Where the company had not tracked — in a disaggregated manner — the results of implementing a particular recommendation, then the savings were quantified through calculation. For example, if, as a result of a process modification, a particular waste stream was eliminated, the savings related to that would be calculated based on the amount of waste generated (as recorded by waste hauler invoices) during a specific time period prior to the modification, as compared to the waste generated during the same period of time following the modification and then normalized to a unit of production.
The cost saving per unit output would then be multiplied by the total production for an annual savings. The same process could be used to calculate GHG savings — using calculated energy savings and the applicable GHG emission coefficient (e.g. kg CO2e/kwh or kg CO2e/L of fuel)
In addition, where participants noted a particular opportunity was not implemented, they were asked to describe the primary barrier and [where possible] what would have helpful in overcoming that barrier. While the qualitative output of these interviews will not be discussed in details as part of this paper, some general conclusion will be drawn from their reposes as they relate knowledge transfer and to the efficacy of related innovations systems.
Specific Program Results
49 of the 54 companies agreed to participate in the interview process. Of those 42 companies had indicated that they had undertaken either one or more of the recommended initiatives that were identified as a result of their participation in the E2PM. 29 were able to provide information that could be linked to a quantifiable saving, either in $ or other material/energy unit5. This represented 53% of applicable participants.
5 Seventeen (17) companies were able to provide data that permitted the calculation of savings in $(CD).
The balance provided data sufficient to calculate material savings or GHG emissions reductions.
|
Of these 49 companies, four (4) indicated that they implemented more initiatives than were actually identified in their assessment and [in some cases] realized greater $ savings than projected (Table 3). Another six suggested they believed that they implemented 67% of the recommendations identified and thirteen noted 33-67%. Nineteen implemented some of the opportunities, but less than 33% of what was identified as potential opportunities. Those remaining companies indicated that they had not yet implemented any of the recommendations. While this could suggest that some companies had therefore not benefited from the program, some companies responded that they recognized the benefit of the recommendations and simply had not implemented those project citing skills and time constraints of their staff.
Table 2: Company Follow up Results

Table 3: Portion of Potential Opportunities Implemented
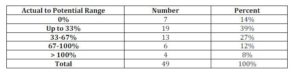
Despite acknowledging either financial or resource-use benefits, as noted not all respondents were able to provide feedback that permitted a quantifiable or calculable saving. Those companies indicated that they were not able to do so for two primary reasons:
- The recommended initiatives were energy or material savings initiatives that could not be quantified due to the aggregated nature of the associated data; or
- The participants implemented recommendations for which they could not provide quantifiable saving but did so because they recognized the inherent benefit of improved resource conservation and/or efficiency. Some examples included fluid recirculation and reuse; the installation of water saving devices in facilities that did not monitor or pay for water use; substitution of chemicals with more benign alternatives; gradual modifications of light fixtures or other equipment to more energy efficient models such that any savings were incremental and not monitored.
The analysis of those that did maintain such data indicated that there has been a significant uptake of the recommendations and the bulk of the participants were able to realize some benefit from their association with the E2PM. Of the $8.2 M identified as potential savings, thus far $2.8 M dollars’ worth of savings (or 34%) have been reported. This represents an average of $57K per responding company and an actual savings of $5.15 dollars for every dollar invested in program delivery.
The GHG emissions savings that were reported by participants of the program totaled 8214 tonnes/annually. In all cases the GHG savings were calculated based on the demonstrated savings in energy units (L of fuel, kWh, m3 of gas) multiplied by applicable GHG emission coefficients.
The opportunities identified for the various participants were very diverse and in many cases very facility specific. Projects included energy-efficiency initiatives such as the replacement of old motors, energy conservation initiatives such as waste heat recovery and energy substitution initiatives such as the replacement of fuel oil with internally produced biogas or biofuels, or the installation of solar walls and geothermal systems.
Some opportunities such as electricity savings through the installation of energy efficient lighting were common recommendations but by no means represented the bulk of the savings. In some cases participants realized energy savings from more than one opportunity.
Table 4 notes the waste diversion/elimination successes that were reported that could be quantified. Unfortunately, in these particular cases while the volumes of material were quantifiable, due to the data management in place within these facilities, calculating the specific cost savings was not straight forward.
Beyond these examples, there were cases where participants reported finding innovative uses for waste materials resulting in a value-add beyond the elimination of tipping fees. In addition, some developed ways to eliminate waste due to process modifications or internal recycling/reuse initiatives. However they had not maintained sufficient data for the savings to be quantified.
Table 5 provides an overview of the potential savings that had been broad before the various participants and the actual impact in terms of the final annual savings that have been realized due to the implementation of these recommendations. It should be noted again that these were only the quantifiable outcomes reported by the participants.
Table 4: Waste Diverted or Eliminated by Company Type
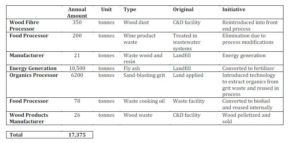
Table 5: Total Identified Annual Savings for Opportunities Implemented
Discussion
It emerged during the interviews that numerous innovations had been implemented that had been identified internally after they participated in the program but due to the nature of the companies data management were unable to provide rigorous numbers related to specific savings in terms of either $ or energy/material — units. Many noted an increased awareness of the potential opportunities related to improved resource efficiency and reported the development of a more resource efficient culture within their facilities. Since their involvement with the program, they had experienced an increase in the interest and capacity of their staff to seek out related innovations. Specific examples include:
- Investigating the feasibility of integrating anaerobic digestion technology into their wastewater system with the intention of using the biogas as a fuel for pre-heating boiler feedwater;
- Discussions with neighbouring businesses regarding the feasibility of supplying excess process waste heat for the purpose of space heating;
- Diverting benign organic material by-products from the municipal waste stream to be used as soil amendment by local farmers;
- Development of by-product synergy [or industrial symbiosis] networks within geographically co-located operations;
- Investment in equipment to transform waste animal fats and vegetable oils into biofuels for internal use and as a secondary income stream not previously exploited; and
- Incorporating technology from an unrelated industry in a new and novel way that resulted in the elimination of up to 75% of a particular material throughput and reduce waste management and transportation costs significantly.
As a result of the goodwill and positive feedback, the EEC researchers and staff were approached to speak at industry and governmental conferences in other jurisdictions. Most notably has been the broader information exchange that evolved within related industrial networks. For example, in May 2010, industry organizations created similarly focused resource efficiency programs for their members.
The development and roll-out of these programs were modeled after the E2PM program. Local regional development authorities have also reached out for support in the development of their own programs to be introduced to their industry and business stakeholders through business outreach programs already in place (CoRDA, 2011).
In addition, participants have demonstrated a willingness (and in some cases an eagerness) to become involved in other initiatives such: a) as providing internships to university students interested in supporting their resource efficiency; b) sending staff to provide guest lecturers on the benefits of resource efficiency to incoming students taking business, resource management or industrial focuses courses; c) sponsoring resource efficiency focused events and workshops designed help continued to disseminate applicable knowledge within the SME sector; and — perhaps most importantly — actively engaging their SME networks at industry events to help build the credibility of such initiative as beneficial to their SME peers.
Implications for Resource Efficiency as Innovation within SMEs
Christensen and Raynor refer to ‘disruptive innovations’ in The Innovator’s Solution (2003). Whereas radical innovations involve significant technical advance (i.e. the type of innovation associated with patents), disruptive innovation is normally associated with a shift in behaviour. While disruptive innovation is typically associated with promoting a ‘disruption’ in the market-place (e.g. providing a product or service that dramatically shifts the market place from its previous status quo), it can be argued that an innovation which acts as a catalyst for behaviour shifts within industrial operations, could also be seen as ‘disruptive’.
For example, if the introduction of resource efficiency to an SME results in a behaviour shift within that SME then the concept was disruptive to the organization. If the shift in one organization catalyzes a similar shift within geographically or sectorally related organizations, the ‘innovation’ has broadened its disruptive capacity to a point that it may be leveraged to promote similar behaviour shifts within the broader SME community.
Bessant et al. (2005), in reviewing the body of literature related to innovation and knowledge transfer, described the notion of a ‘tipping point’ at which the rate that an idea or innovation transmits within a community accelerates rapidly — beyond this point the idea, message or behaviours spread like a virus — thereby disrupting previous norms at scale.
Disruptive activity has long been recognized as an important catalyst for economic development as it involves the creation of new industries and the destruction of others (Schumpeter, 1934). The role of disruptive innovation within SMEs to enable them to meet the challenge of sustainability has also emerged in the green innovation literature (Vickers, et al., 2009; Brown et al., 2007). Where sustainability is the emphasis, the concept of innovation as a simple, linear process that is driven by scientific discovery or market demands has limited merit. More sophisticated and complex models that emphasize interactive knowledge transfer between businesses, learning institutions, supply-chains, and regulatory regimes described previously (Hughes and O’Regan, 2009; Huggins and Johnston, 2009; McAdam et al., 2010; Parrilli et al., 2010) are more applicable.
In this instance, the disruption supports two of the three pillars of knowledge transfer by promoting: a) good linkages with external sources of knowledge (both codified and tacit); and b) an external culture that supports innovation (Ashford et al., 2002; Gray, 2006; Hoffren and Apajalahti, 2009; McAdam et al., 2010).
Regardless of the intention of the innovation progress, innovation itself arises in one of two ways: a) through access to or generation of new knowledge or; b) through the combination of existing pieces of knowledge in novel, “entrepreneurial” ways (Schumpeter, 1934). What is more commonly contested is our understanding of how knowledge used within innovation processes originates.
The large body of literature related to innovation and the various actors within the process (Wang and Ahmed, 2004; EFQM, 2005; Francis and Bessant, 2005; Ramsden and Bennett, 2005; Gray, 2006; Sparrow et al., 2006; Zhang et al., 2006; Parrilli et al., 2008; Parrilli et al., 2010; Varis and Littunen, 2010) make it clear that the level of success found within different innovation systems varies widely, as do the agents within each system.
The literature has also demonstrated that there is a need to increase the level of knowledge specifically within SMEs regarding technologies and strategies that can be applied to improve their resource efficiency — particularly around the ‘business case’ for doing so (Côté et al., 2006; Masurel, 2007; Borga et al, 2009). Any innovation system designed to support knowledge transfer within the SME context must overcome the barriers to knowledge integration and application.
Conclusion
This research has focused on one particular mechanism through which higher education institutions (HEI) could play a role in this transfer and application of knowledge as it related to green innovation, specifically resource efficiency. Through the various activities framed within the E2PM program, resource efficiency related knowledge was transferred to SME manufacturers in Nova Scotia resulting in behaviour changes and innovations that lead to improved environmental performance and economic benefit.
Creating a space within a HEI where knowledge is accessible, practical and delivered in a context meaningful to SMEs — appears to be a novel approach within the context of environmental innovation. If we refer back to the three pillars necessary for knowledge transfer within SMEs, this process has impacted positively on all three points:
- Linkages to Sources of External Knowledge An easy portal was provided for SMEs to access information such as fact sheets, business cases, and best practice documents that were developed with a practitioner focus such that there were easily understood and in the appropriate context for SME manager. Knowledgeable staff and researchers were always available to answer questions, and were also publically visible (and therefore accessible) as a result of their participation in industry focused events. This supported ‘stable’ SMEs (Zhang et al, 2006) by providing contextualize information that could they could directly link to their own operations, thus playing to their need for hands-one or experiential learning. This also supported SMES who were transitioning to a more ‘innovative’ stance (Zhang et al, 2006) in providing them with the information and interaction needed to support their learning processes.
- External Culture That Supports Resource Efficiency Promoting success stories and demonstrated business cases that resulted within the Nova Scotia SME sector, has promoted a gradual shift in the sector toward higher levels of acceptance and increased credibility regarding the benefits of eco-efficiency related innovation. Participants use their innovations and successes as for marketing purposes; many provided testimonials to be used by the EEC in public forums. Numerous government departments and industry associations have requested that industry focused presentation be delivered – related to the benefits of resource efficiency and related strategies such as by-product synergies and renewable energy options. Therefore as this ‘fringe’ information becomes more accepted and mainstream it supports the development of absorptive capacity within stable SMEs driving a transition from stable to more innovative in nature. The legitimacy around the utility and benefits of improved resource efficiency becomes more accepted or ‘tacit’ within their operations. Changes to norms and attitudes become easier to accept internally as a result of this transition in the external culture.
- Internal Culture That Is Capable of Integrating and Adjusting to New Ideas The goodwill and credibility realized by the EEC transmits through the SME sector by ‘word of mouth’ to the point that new SMEs and business networks contact the university for support – such as the delivery of internal workshops and training sessions. The demand is coming from within individual organizations that wish to better understand the potential benefits that resource efficiency can provide. In addition, SMEs are better able to connect with student groups who — as part of their curriculum — can conduct research into sustainability problems faced by the business and try to provide preliminary solutions or at least expose the business to new information that they themselves may be able to then capitalize on. This interest has been driven by the SME sector.
The results described in this paper demonstrate the potential impact of such an approach for enhancing HEI contributions to the environmental and resource efficiency innovation systems involving SME manufacturers. It is suggested that this style of interaction could be useful to other HEIs to increase their contribution to regional innovation systems that: a) that have significant numbers of SMEs; and b) include sustainability objectives, for example GHG emission reductions, waste minimisation and energy efficiency.
For example, many HEIs have entrepreneurship centers that operate both as research units and as portals for interaction between the institution (its staff and students) and the private sector. Few have an explicit environmental mandate, but arguably the advice they provide to SMEs on business development and competitiveness will be increasingly inadequate without an explicit environmental dimension. As such, a more effective model could be built upon the premise of acting as a disruptor to the status quo. This would be accomplished by actively delivering ‘fringe’ knowledge held within HEI (what is often considered ‘common knowledge’ by the HEI’s themselves) — in a manner that is acceptable and easy to understand by those SMEs.
It could allow these entrepreneurship centres to be expanded, integrating an inter-disciplinary space where multiple academic disciplines — such as Business, Management and Engineering — could contribute. This in turn, could create the opportunity to support transformative scholarship, knowledge creation and capacity building —capabilities which are urgently needed from HEIs if they are to play a role in addressing the issues of resource efficiency and sustainability within local and regional economies, and contribute to national and international policy objectives.
Acknowledgements
The author would like to acknowledge the support from Gerry Archibald and Charles Harrington of the Eco-Efficiency Centre (EEC) whose contributions were instrumental to the completion of this research. The data analysis and manuscript preparation was possible with the support of SSHRC through a public outreach grant (file #605-2009-0025)
References
Ashford, N., Hafkamp, W., Prakke, F. & Vergragt, P. (2002). ‘Pathways to Sustainable Industrial Transformations: Co-Optimising Competitiveness, Employment and Environment,’ MIT Press, Cambridge.
Bessant, J., Phelps, B. & Adams, R. (2005). “A Review of the Literature Addressing the Role of Knowledge and Expertise at Key Stages of Business Growth and Development: Final Report,” Cranfield Collection of E-Research. Cranfield University [Online], [Retrieved July 20, 2011],https://dspace.lib.cranfield.ac.uk/bitstream/1826/1036/4/Rev_of_Lit_Business_Growth_Final_Report_2005.pdf
Publisher
Bessant, J. & Tidd, J. (2007). Innovation and Entrepreneurship, John Wiley, Chichester.
Publisher – Google Scholar
Borga, F., Citterio, A., Noci, G. & Pizzurno, E. (2009). “Sustainability Report in Small Enterprises: Case Studies in Italian Furniture Companies,” Business Strategy and the Environment, 18(3), 162 — 176.
Publisher – Google Scholar
Brown, J. Hendry, C. & Harborne, P. (2007). “Developing Radical Technology for Sustainable Energy Markets: The Role of New Small Firms,” International Small Business Journal, 25(6), 603-629.
Publisher – Google Scholar – British Library Direct
Chertow, M. R. (2000). “Industrial Symbiosis: Literature and Taxonomy,” Annual Review of Energy and the Environment,25, 313-337.
Publisher – Google Scholar – British Library Direct
Christensen, C. M. & Raynor, M. E. (2003). The Innovator’s Solution, Harvard Business School Press, Boston.
Publisher – Google Scholar
Corda. (2012). ‘Greening Your Business,’ Colchester Regional Development Authority. [Retrieved Dec 12, 2011], http://www.corda.ca/greenbusiness/
Cote, R., Booth, A. & Louis, B. (2006). “Eco-Efficiency and SMEs in Nova Scotia, Canada,” Journal of Cleaner Production, 14, 542-550.
Publisher – Google Scholar
Desimone, L. D. & Popoff, F. (1997). ‘Eco-Efficiency: The Business Link to Sustainable Development,’ The MIT Press, Cambridge.
Google Scholar
Drake, F., Purvis, M. & Hunt, J. (2004). “Meeting the Environmental Challenge: A Case of Win-Win or Lose-Win? A Study of the UK Baking and Refrigeration Industries,” Business Strategy and the Environment 13(3): 172-185.
Publisher – Google Scholar – British Library Direct
Eco-Efficiency Centre (2009a). “About us,” Dalhousie University’s Eco-Efficiency Centre. [Retrieved July 20, 2011]http://eco-efficiency.management.dal.ca/About_Us/
Publisher
Eco-Efficiency Centre (2009b). ‘Case Studies (For the Business Case of Sustainability),’ Dalhousie University’s Eco-Efficiency Centre [Retrieved July 20, 2011], http://eco-efficiency.management.dal.ca/Publications_%26_Resources/Case_Studies.php
Eco-Efficiency Centre (2010). ‘Success Stories,’ Dalhousie University’s Eco-Efficiency Centre. [Retrieved July 20, 2011] http://eco-efficiency.management.dal.ca/Publications_%26_Resources/Success_Stories.php
EFQM (2005) ‘The Business Excellence Model for SME,’ European Foundation for Quality Management, Brussels.
Etzkowitz, H. (2008). The Triple Helix: University—Industry—Government Innovation in Action, Routledge, New York.
Publisher – Google Scholar
Etzkowitz, H. & Leydesdorff, L. (1997). “Universities and the Global Knowledge Economy: A Triple Helix of University-Industry-Government Relations,” Lavoisier S.A.S., Paris.
Publisher – Google Scholar
Etzkowitz, H. & Leydesdorff, L. (2000). “The Dynamics of Innovation: From National Systems and ‘Mode 2’ to a Triple Helix of University-Industry-Government Relations,” Research Policy 29 (2), 109-123.
Publisher – Google Scholar
Fiol, C. M. & Lyles, M. A. (1985). “Organizational Learning,” The Academy of Management Review 10(4), 803-813.
Publisher – Google Scholar
Francis, D. & Bressant, J. (2005). “Targeting Innovation and Implications for Capacity Development,” Technovation 25,171-183.
Publisher – Google Scholar
Gorman, G., Hanlon, D. & King, W. (1997). “Some Research Perspectives on Entrepreneurial Education, Enterprise Education and Education for Small Business Management,” International Small Business Journal, 15(3), 56-77.
Publisher – Google Scholar – British Library Direct
Gray, C. (2006). “Absorptive Capacity, Knowledge Management and Innovations in Entrepreneurial Small Firms,”International Journal of Entrepreneurial Behaviour and Research, 12 (6), 375-387.
Publisher – Google Scholar – British Library Direct
Gunasekara, C. (2006). “Reframing the Role of Universities in the Development of Regional Innovation Systems,”Journal of Technology Transfer, 31 (1), 101—113.
Publisher – Google Scholar – British Library Direct
Hansen, O. E., Sondergard, B. & Meredith, S. (2002). “Environmental Innovations in Small and Medium Sized Enterprises,” Technology Analysis and Strategic Management, 14(1), 37-56.
Publisher – Google Scholar – British Library Direct
Hart, S. L. (1995). “A Natural-Resource-Based View of the Firm,” Academy of Management Review, 20(4), 986—1014.
Publisher – Google Scholar – British Library Direct
Hart, S. L. (1997). “Beyond Greening: Strategies for a Sustainable World,” Harvard Business Review, 75, 66—76.
Publisher – Google Scholar – British Library Direct
Hart, S. L. & Sharma, S. (2004). “Engaging Fringe Stakeholders for Competitive Imagination,” Academy of Management Executive, 18(1), 7-18.
Publisher – Google Scholar – British Library Direct
Hawken, P., Lovins, A. & Lovins, L. H. (1999). ‘Natural Capitalism: Creating the Next Industrial Revolution,’ Little, Brown, & Co, New York.
Google Scholar
Hillary, R. (2000). Small and Medium-Sized Enterprises and the Environment: Business Imperatives, Greenleaf Publishing, Sheffield.
Publisher
Hoffren, J. & Apajalahti, E. L. (2009). “Emergent Eco-Efficiency Paradigm in Corporate Environmental Management,”Sustainable Development, 17, 233-243.
Publisher – Google Scholar
Howells, J. (1996). “Tacit Knowledge, Innovation and Technology Transfer,” Technology Analysis and Strategic Management, 8(2), 91-106.
Publisher – Google Scholar – British Library Direct
Howells, J.R. L. (2002). “Tacit Knowledge, Innovation and Economic Geography,” Urban Studies, 39 (5/6), 871-884.
Publisher – Google Scholar – British Library Direct
Huggins, R. & Johnston, A. (2009). “Knowledge Networks in an Uncompetitive Region: SME Innovation and Growth,”Growth and Change, 40(2), 227-259.
Publisher – Google Scholar
Hughes, T., O’Regan, N. & Sims, M. A. (2009). “The Effectiveness of Knowledge Networks: An Investigation of Manufacturing SMEs,” Education and Training, 51(8/9), 665-681.
Publisher – Google Scholar
Könnölä, T. & Unruh, G. C. (2007). “Really Changing the Course: The Limitations of Environmental Management Systems for Innovation,” Business Strategy and the Environment, 16(8), 525-537.
Publisher – Google Scholar – British Library Direct
Korhonen, J., von Malmborg, F., Strachan, P. A. & Ehrenfeld, J. R. (2004). “Management and Policy Aspects of Industrial Ecology: An Emerging Research Agenda,” Business Strategy and the Environment, 13(5), 289-305.
Publisher – Google Scholar – British Library Direct
Leydesdorff, L. & Etzkowitz, H. (1998). “The Triple Helix as a Model for Innovation Studies,” Science and Public Policy25(3), 195-203.
Publisher – Google Scholar – British Library Direct
Lovins, H. (2008). Rethinking Production, State of the World 2008: Innovations for a Sustainable Economy, Worldwatch Institute, New York, 32-44.
Publisher
Masurel, E. (2007). “Why Smes Invest in Environmental Measures: Sustainability Evidence from Small and Medium-Sized Printing Firms,” Business Strategy and the Environment, 16 (3), 190-201.
Publisher – Google Scholar – British Library Direct
Mcadam, R., Moffett, S., Hazlett, S. A. & Shevlin, M. (2010). “Developing a Model of Innovation Implementation for UK Smes: A Path Analysis and Explanatory Case Analysis,” International Small Business Journal, 28(3), 195-214.
Publisher – Google Scholar
McDonough, W. & Braungart, M. (2002). Cradle to Cradle: Remaking The Way We Make Things, North Point Books, New York.
Publisher – Google Scholar
Parker, C., Redmond, J. & Simpson, M. (2009). “A Review of Interventions to Encourage SMEs to Make Environmental Improvements,” Environment and Planning C: Government & Policy, 27(2), 279-301.
Publisher – Google Scholar
Parrilli, M. D., Aranguren, M. J. & Larrea, M. (2010). “The Role of Interactive Learning to Close the “Innovation Gap” In SME-Based Local Economies: A Furniture Cluster in the Basque Country and its Key Policy Implications,” European Planning Studies, 18(3), 351-370.
Publisher – Google Scholar
Parrilli, M. D. & Sacchetti, S. (2008). “Linking Learning and Governance in Networks and Clusters: Key Issues for Analysis and Policy,” Entrepreneurship and Regional Development, 20(4), 387-408.
Publisher – Google Scholar
Porter, M. E. & Van Der Linde, C. (1995). “Green and Competitive: Ending the Stalemate,” Harvard Business Review,Sept/Oct, 120-137.
Publisher – Google Scholar – British Library Direct
Ramsden, M. & Bennett, R. (2005). “The Benefits of External Support to SMEs: “Hard” Versus “soft” Outcomes and Satisfaction Levels,” Journal of Small Business and Enterprise Development, 12 (2), 227-243.
Publisher – Google Scholar
Revell, A. & Blackburn, R. (2007). “The Business Case for Sustainability? An Examination of Small Firms in the UK’s Construction and Restaurant Sectors,” Business Strategy and the Environment, 16(6), 404-420.
Publisher – Google Scholar – British Library Direct
Schmidheiny, S. (1992). Changing Course: A Global Business Perspective on Development and the Environment, MIT Press, Cambridge.
Publisher – Google Scholar
Schumpeter, J. (1934). ‘Theory of Economic Development. An Inquiry into Profits, Capital, Credit, Interest, and the Business Cycle,’ Harvard University Press, Cambridge. Reprint 1983: Transaction, Inc.
Google Scholar
Senge, P. M., Carstedt, G. & Porter, P. L. (2001). “Innovating Our Way to the Next Industrial Revolution,” MIT Sloan Management Review, 42(2), 24-38.
Publisher
Sparrow, J., Mooney, M. & Lancaster, N. (2006). “Perceptions of a UK University as a Knowledge Intensive Business Service Enhancing Organizational and Region Service Innovation,” International Journal of Business Innovation Research, 1(1/2), 191-203.
Publisher – Google Scholar
Sparrow, J., Tarkowski, K., Lancaster, N. & Mooney, M. (2009). “Evolving Knowledge Integration and Absorptive Capacity upon University/Industry Interaction within a University,” Education and Training, 51(8/9), 648-664.
Publisher – Google Scholar
Springett, D. (2009). ‘Education for Sustainability in the Business Studies Curriculum: Idealogical Struggle,’ Sustainability Education: Perspectives and Practice across Higher Educations. Jones, P. et al. (Eds), Chapter 5, 75-88.
Stern, N. (2007). The Economics of Climate Change: The Stern Review, Cabinet Office — HM Treasury. Cambridge University Press, Cambridge.
Publisher – Google Scholar
Studer, S., Welford, R. & Hills, P. (2006). “Engaging Hong Kong Businesses in Environmental Change: Drivers and Barriers,” Business Strategy and the Environment, 15 (6), 416-431.
Publisher – Google Scholar – British Library Direct
Tosey, P., Visser, M. & Saunders, M. N. K. (2011). “The Origins and Conceptualizations of ‘Triple-Loop’ Learning: A Critical Review,” Management Learning.
Publisher – Google Scholar
Varis, M. & Littunen, H. (2010). “Types of Innovation, Sources of Information and Performance in Entrepreneurial SMEs,”European Journal of Innovation Management, 13(2), 128-154.
Publisher – Google Scholar
Vickers, I., Vaze, P., Corr, L., Kasparova, E. & Lyon, F. (2009). SMEs in a Low Carbon Economy, Centre for Enterprise and Economic Development Research, London.
Publisher – Google Scholar
Wang, C. L. & Ahmed, P. K. (2004). “Leveraging Knowledge in the Innovations and Learning Process at GKN,”International Journal of Technology Management, 27, 674-688.
Publisher – Google Scholar – British Library Direct
WBCSD (2000). ‘Eco-Efficiency: Creating More Value with Less Impact,’ Conches, Geneva.
Google Scholar
Weizsacker, E., Lovins, A. B. & Lovins, H. L. (1997). ‘Factor Four: Doubling Wealth, Halving Resource Use,’ Earthscan, London.
Google Scholar
Wheeler, D., Zohar, A. & Hart, S. (2005). “Educating Senior Executives in a Novel Strategic Paradigm: Early Experiences of the Sustainable Enterprise Academy,” Business Strategy and the Environment, 14(3), 172—185.
Publisher – Google Scholar
Williamson, D., Lynch-Wood, G. & Ramsay, J. (2006). “Drivers of Environmental Behaviour in Manufacturing SMEs and the Implications for Csr,” Journal of Business Ethics, 67, 317—330.
Publisher – Google Scholar – British Library Direct
Zahra, S. A. & George, G. (2002). “Absorptive Capacity: A Review, Reconceptualization and Extension,” Academy of Management Review, 27(2), 195-203.
Publisher – Google Scholar – British Library Direct
Zhang, M., Macpherson, A. & Jones, O. (2006). “Conceptualizing the Learning Process in SMEs: Improving Innovation through External Orientation,” International Small Business Journal, 25, 299-323.
Publisher – Google Scholar – British Library Direct